Differences between electronics manufacturers
- Greg Ross
- Feb 5, 2015
- 6 min read
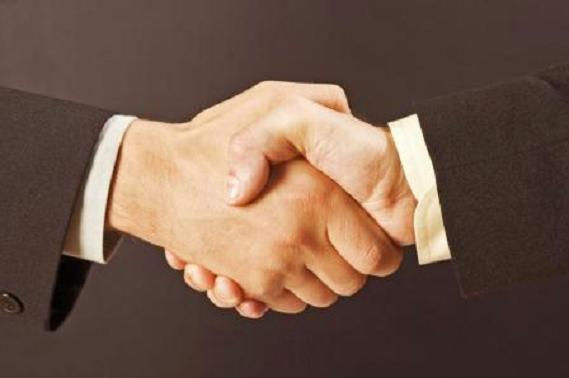
I was reading an article the other day entitled "Six things electronics companies should NOT do in the future" and was pondering the relevance to the general Australian electronics scene. Much of what is written is pointed towards large multinational OEM's but there are particular points which I would like to expound on which do have particular relevance to the Australian electronics scene as well as adding some of my own. Some points are brought up in this article are best read there and I will not attempt to repeat here.
Electronics based OEM's are all attempting be as different as possible with their own products however for some reason they find it necessary to follow the others when it comes to basic operational issues such as:
Selecting a CEM
Internal Process Controls
Equipment Selection
Invariably someone reads a single article and comes to a conclusion that it suits their purpose and acts on it. This article was probably written with the authors end motives in mind so it would be most likely a slanted view and could never take into consideration the readers unique situation. These types of articles are actually "Infomercial's" for want of a better word, simply put, a way to sell the authors story for his gain or motive, not yours. These articles are written by vendors of the equipment, software or processes which the author would sell, make income or benefit from in some fashion. What happens is the person implementing these things are actually reducing the uniqueness of your corporate structure.
A perfect example of this is in the form of software. Your company purchases a piece of software which purports to be the be all and end and of all of its class and "future-proof". Only after an extremely painful implementation process do you now realise that all of your internal process and practices are now dictated to operate the way the software tells you to perform them and potentially not the way you would like to run them. You have essentially turned over your company processes this software controls to a software company. Does this sound familiar or more to the point, the way you would like it to be?
Now I am not suggesting that we not use software for what it is, I am saying that simply because generic software says that it likes to function a certain way does not mean your company should restrict itself. Electronics Manufacturing is an ever moving target which needs to be dissected, understood and re-analysed constantly. What worked before will not necessarily work now, it can only be used as a basis to evolve from. Processes and procedures must adapt to whatever situation they encounter in the future. It is a fact that business success requires innovation in all aspects of your business. This means internally you must be unique to match your situation and manufacturing style. That is why it is intriguing how a lot of businesses follow others to base their particular success on.
Some examples are:
Outsourcing to China because it is cheaper
There is a perception that unless you manufacture in China you have not "made it". A lot of companies believe that simply because a quote from a Chinese CEM is cheaper it is the right thing to do. It is extremely difficult for one to actually calculate the true manufacturing cost of outsourcing to a long distance CEM. When the actual labor cost of most products as a ratio to selling cost is approximately 5% then it seems ludicrous to attempt to save a potential 2.5% and risk your companies cash flow and product reputation in the process. Even that estimated 2.5% savings is a debatable subject as to whether it could be achieved. On one end of the corporate structure you have a manufacturing division who has a total of 5% flexible labor costs in which to save money from and at the other end you have a Sales department willing to throw away a 10 or even 25% discount to almost anyone who asks. But all focus seems to be on this 5% and how it might become 2.5%. There are some sectors that will benefit from outsourcing to China namely mobile phones, etc. These are sectors in a situation where the labor content have a higher percentage of the overall sales price and their respective margins are so low that it warrants these savings.
Being "Politically Correct" instead of honest In a business relationship
it is of utmost importance the there is clear concise dialogue at a level in which all parties comprehend. Manufacturing is complex enough without putting ego's into the mix or over complicating the issues. Both parties (OEM and CEM) must work tirelessly and honestly together to achieve the results that both desire.
eg:An OEM produces a 100 page document detailing everything in extremely long winded wordy descriptions concerning the manufacture of a product which ends up being confusing to the recipient (CEM) more than helping. These are normally additive type documents. By this I mean that these start out being a sensible specification in size and description but somewhere along the evolutionary path of this product or a previous product some problem in manufacturing happened and these irregularities prompted the author to add these to this specification. Before you know it this more of a history of the problems encountered and how NOT to manufacture the product instead of how to manufacture it. The basic specification is lost in the detail. The OEM now is able to pin "blame" on the CEM if any instance contained in the document deviates from the "written word". In fact what happens is that the recipient then uses this very document as an excuse for something that went wrong because it wasn't written there which in turn prompts the writer to add this instance further confusing the issue.
The OEM and CEM must work together to ensure that products or services and specified to what needs to be achieved, not how or what not to be. Each CEM will have their own processes and procedures in place to ensure this happens however when problems do arise, and they will, there must be latitude given so the CEM can evolve his process to take care of issue and not be required to add new processes as "bandaid" solutions.
Invention of new "Initiatives" that complicate things
A "New" initiative is normally just a knee jerk reaction to an issue that has arisen and someone has decided to institute a new regime or system to detect this issue in the future instead of solving the root cause of the defect. In manufacturing this is similar to instituting a new inspection to combat a inherent problem in manufacturing instead of simply fixing the problem. These "New Initiatives" can take the form of anything being paperwork, accounting procedures or QA procedures to name a few. The basic similarity is that they are all additive processes, meaning they consist of additional control systems instead of replacement systems. It is a failure to admit the system is not working and instituting a more appropriate one.
eg: In SMT there are constant problems with the amount of paste deposited onto PCB's resulting in badly assembled PCB's. Investigations ensue and the consensus result is that an AOI must be purchased to find all of these problems, customers will be lost unless problems go away. An AOI is purchased, an engineer is hired to program it and because the AOI is detecting so many soldering defects that new rework equipment and staff are required. Everyone pats themselves on the back because the problem has been solved and the customer is no longer complaining. This is the proverbial additive process I was referring to. The correct alternative could have been to correct the problem at the screen printing stage where the problem was first generated. This would have enabled the PCB to be produced defect free, right from the start without adding expensive inspection steps into the process. I am not saying the AOI machines are not effective in their own right but to use them as a solution rather than a means to analyse the problem is wrong.
The point of this discussion is that Electronics Manufacturers need to be creative, adaptive and innovative when it comes to manufacturing their respective products. Their business is normally based on a unique product with the success of the company hinging on this very innovative aspect. Once the product hits the manufacturing cycle there is a distinct shift in the creative thinking of the organisation and the process becomes a money saving exercise. The expression "you get what you pay for" really is true when it comes to manufacturing. It is possible to attain savings by vying suppliers against each other but normally what you are left with is the lowest cost from a supplier that probably does not care if you come or go because they are not making any money anyway, so their service will suffer. Deliveries, quality and service levels drop to a point that your company has serious manufacturing or delivery problems. All businesses must make money to survive, a fair price level must be attained for both the supplier and the customer in a relationship for sustained viability.
If quality, on time delivery and consistency in manufacturing cannot be achieved then it won't matter how innovative your product is, how good your sales people are, what color your logo is, you will not succeed. Manufacturing is not simply about dictating to the CEM, it requires an understanding of issues and proactive involvement.
Greg Ross
Circuitwise P/L
Comments